We go the extra (sea)mile for you –
in the wake of decades of experience.
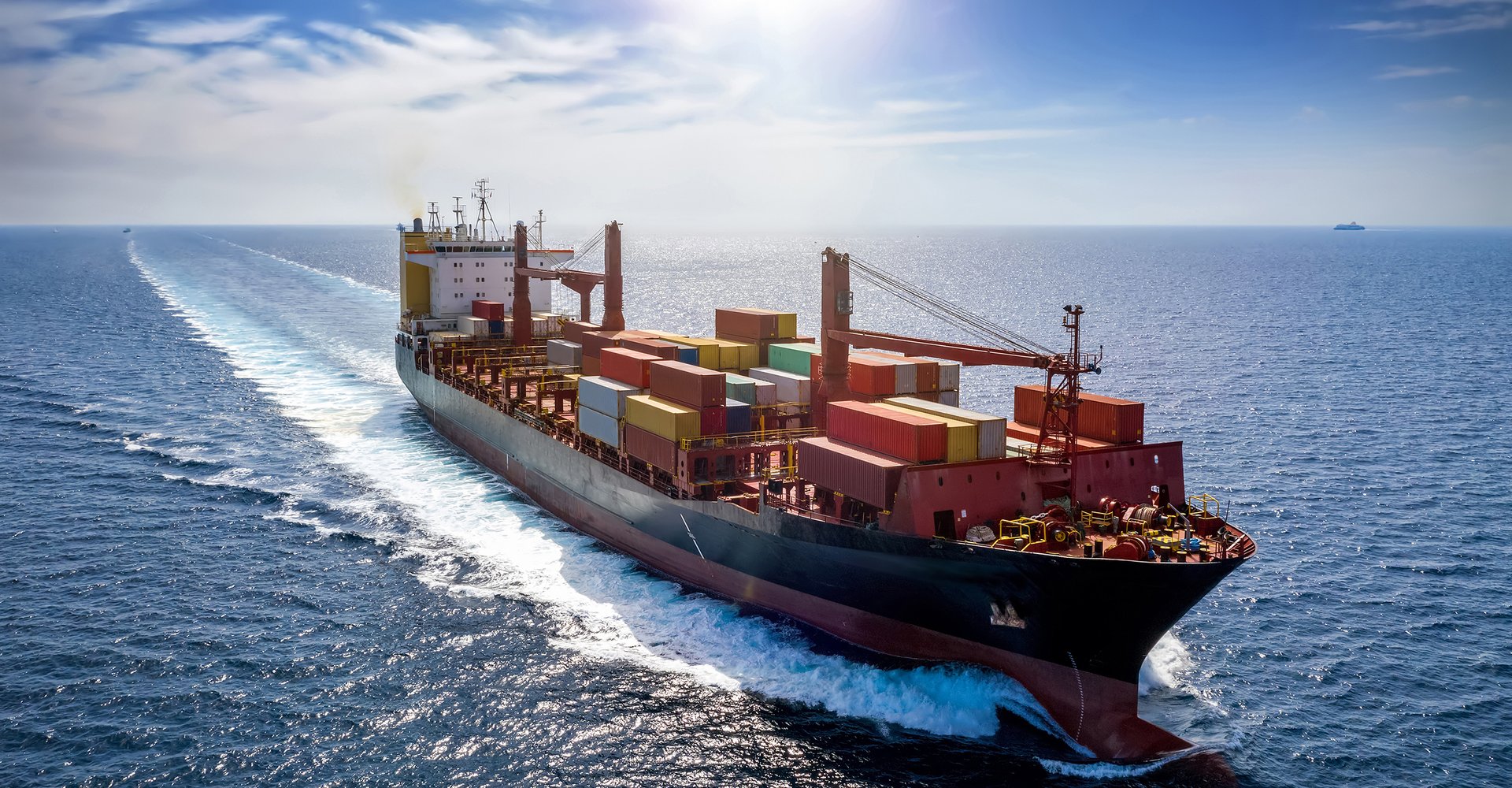
Engines
There are hardly any landing and contact surfaces, and end faces that we cannot machine on engines! These can be, e.g., liner guidings, crank- and/or main bearing journals as well as bearing alley on main or auxiliary engines, bearing shields and bearing bushings on attached generators or other components. Basically, we can be on site quickly with the right tools and machining equipment to fix your problem.
Below you will find a few typical repair examples:
Propulsion
The machining of bearing-, contact surfaces and end faces of the entire drive train, from the engine (whether with or without gearbox) to the stern tube (including its sealing) and the drive shaft is just as much a part of our daily work as the processing of contact surfaces and end faces on variable pitch propellers and the spindling of holes for retaining bolts, including thread renewal.
Examples of repairs are as follows:
Cranes
During operation, shipboard cranes are subject to high loads on the bearings of the rope sheaves and the slewing ring. Whether the bushings of the rope sheave shafts or the bearing surface of the slewing ring: We can work on all end faces, sealing-, contact- and bearing surfaces on your cranes as well as on your grabs of the loading/unloading gear.
Below please find examples of repair areas:
Gearboxes
The teeth need to mesh perfectly again? We make sure of that for you. Whether on bearing guidings of the gears, bearing bushings, complete bearings in the gearbox or the corresponding shafts, on the housing or the foundation mountings outside: we machine and polish on your premises, in the case of major damage we support individual components and get the system running again.
Here you can find exemplary repairs:
Steering
Whether on rudder trunk, rudder engines, rudder shafts or other components of your steering system – we will get your ship back on course with mechanical machining on site. If you experience such a severe damage that there is not enough material left to turn to the new correct installation dimension, we’ll solve this problem with build-up welding or a bushing.
The following are examples of typical repair applications:
Winches
Whether bollard pull winches, combined windlass/mooring winches, mooring winches and coupling winches – we can also machine, measure and align the bearings, shafts, bushings and foundations. If required, we can also manufacture the bushings and supply the bearings.
In the example of this bollard pull winch, the bearings were bored out on both sides and new bearing bushing were inserted:
Contact us now
A safe haven for every problem:
Those who work with us benefit in several ways.
Time
savings
Low dis-
assembly effort
Cost
savings
Certified
methods
Sustainability
through repair
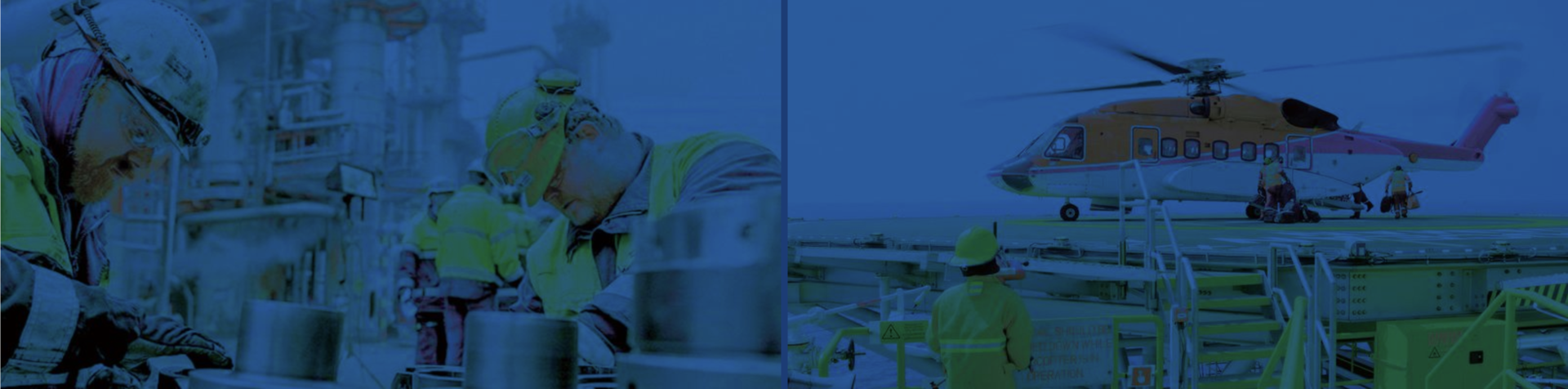
With lots of expertise, passionately inventive and uncompromisingly team-oriented: that's how we are positioned.
With around 200 employees, we are the largest company in the Metalock Engineering Group. Our affiliation with this group ensures that we have worldwide networking and cooperation with experienced specialists from various fields in order to be able to successfully carry out even the most demanding projects. For our assignments, we use machines that we develop in-house, continuously optimize and use exclusively ourselves.
Our clients include corporate groups as well as medium-sized and small companies. How our teams repair the largest machines with a great deal of know-how and highly specialized tools convinces customers from all industries – for example, the automotive, steel, cement, paper and chemical industries, mechanical engineering, energy supply and, of course, shipping. In addition to our technical knowledge and expertise, they appreciate the short reaction times until our specialists are deployed and they are ready to work around the clock.
For more information about Metalock Engineering Germany, please visit: www.metalock.de
Our services
- Mobile machining in industry and marine
- Laser metrology
- Metalock-Repairs
- Welding
- Machine overhauls
- Mechanical manufacturing
- Damage analysis and assessment
- Strength calculations / FEM analyses
- Reverse Engineering
Our locations in Germany
Contact us now
This is how you use our services:
We will be happy to inform you in advance or help you immediately in case of an emergency. Do not hesitate to contact us. You can reach us via contact form or at onsite-machining-maritime@metalock.de. In urgent cases, please use our 24-hour emergency assistance number.